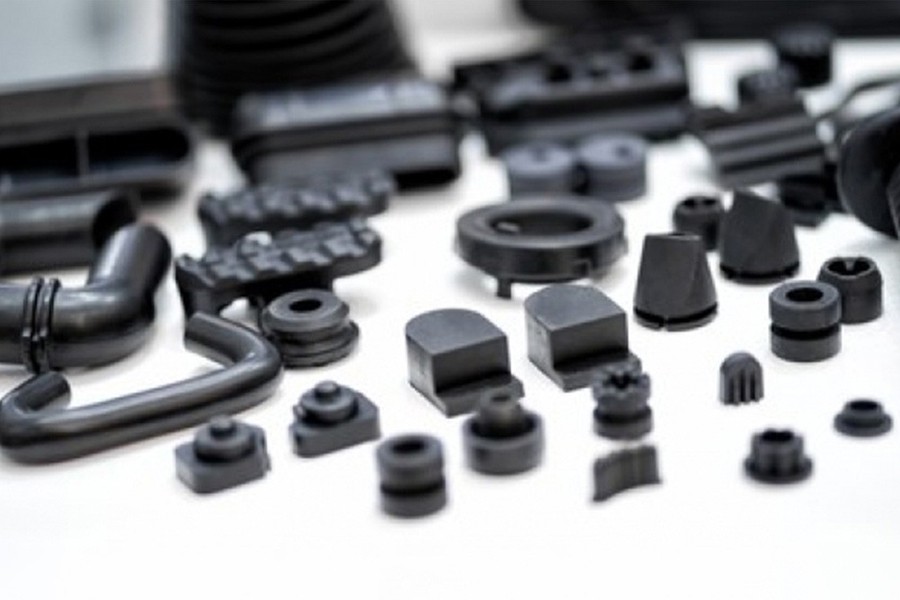
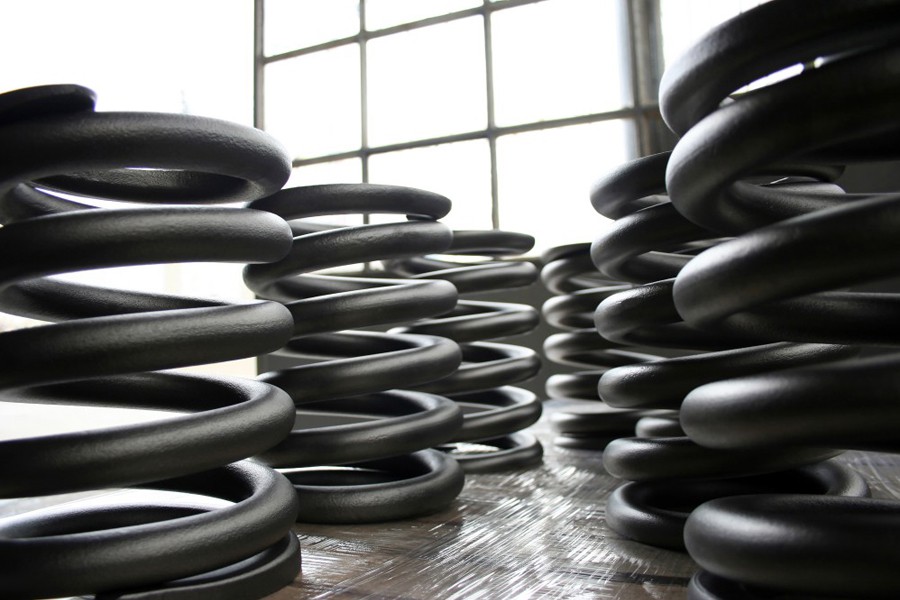
Phosphating is the process of coating a crystalline metal phosphate layer (zinc, iron, manganese, calcium) on a steel or on the surfaces of other metals such as zinc, aluminum.
Phosphate coating process, to increase corrosion resistance (automobile bodies), to create decorative appearances (white goods), to form a corrosion protection layer (suspension elements), to obtain a lubricating layer in cold deformation applications of steels (cold forged parts), primer for adhesion of rubbers It is used for purposes such as creating a material, creating a friction-reducing layer (gearbox equipment).
Gear parts interact with metal-to-metal contact during operation due to geometrical reasons and insufficient lubrication of all surfaces. This contact causes rapid wear of the gears.
In order to solve this problem, manganese phosphate crystals are formed on the gear surface, increasing the wettability of the part surface and improving the oil holding feature.
The phosphating process creates an oil-retaining porous structure on the surface with this crystal structure, ensuring the preservation of slip properties in overloads. Thus, overheating in the gear gears and expansion due to heating are prevented due to the reduction of friction.
Phosphate coating process is a widely used method in the automotive industry due to these well-known functions.
Before coating, it is necessary to create roughness on the surface with the help of chemicals.
Depending on the depth of this created roughness, the morphology of the coating changes.
The oil holding capacity of the surface varies according to the morphological structure on the surface.
The parameters of the baths in the coating process can be adjusted according to the desired surface quality.
The strength, hardness or machinability of the original material is not affected by the phosphating operation.
It performs better than other phosphate applications in mechanisms involving metal-metal contact, its color is close to black.