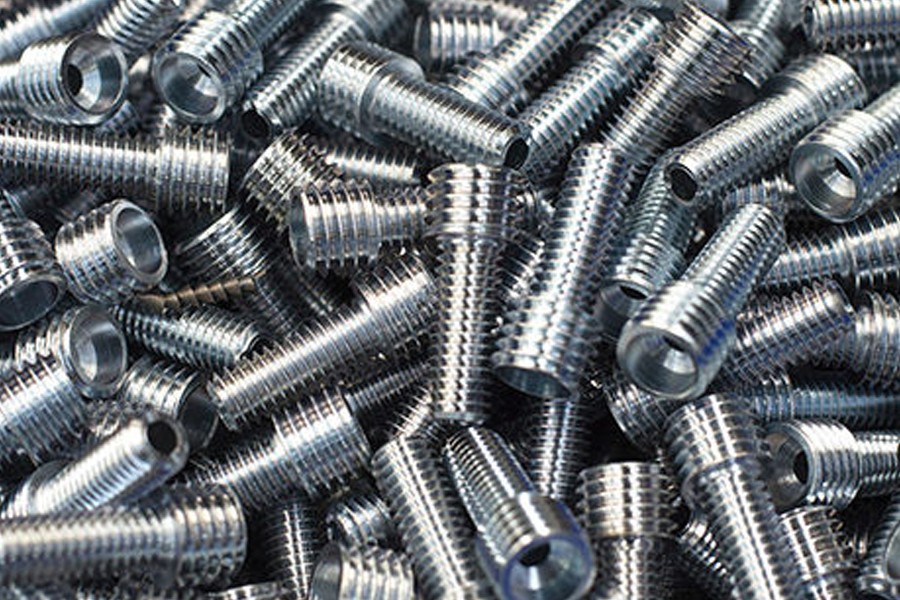
Çinko kaplamalar çelik parçaların korozyondan korunması için yaygın olarak kullanılmaktadır.
Bazı şartlar altında saf çinko kaplamaların sergiledikleri korozyon dayanımı yetersiz kalmaktadır.
Çinkoyu daha soy metallerle alaşımlandırmak kaplamanın çözünme hızını azaltmaktadır.
Kobalt, nikel, demir gibi elementlerle alaşımlandırılan çinko, saf haline göre
daha yüksek korozyon dayanımı sağlar.
Tüm çinko alaşımlı kaplamalar arasında en çok rağbet gören kaplama çinko-nikel kaplamalardır.
Bunun sebebi diğerlerine göre daha yüksek korozyon dayanımı ve termal kararlılık sergilemesidir.
Çinko-nikel kaplamalar üstün özellikleri sayesinde otomotiv, havacılık ve savunma sanayinde sıklıkla kullanılmaktadır.
Çinko-nikel alaşımları elektrolizle kaplanmış çinko kaplamaların en yüksek korozyon direncine sahiptir.
Bu alaşımlar 5-15% aralığında nikel içerir. Bu oranın üzerine çıkıldığında, çelikten daha soy hale gelir ve
fedakar koruma özelliğini kaybeder.
Çinko-nikel alaşımların korozyon direnci, nötral tuz testinde kırmızı pas fenomeninin 1000 saat ve üzerinde gerçekleşmesi potansiyeli taşır.
Çinko-nikel kaplamalar üzerine yapılan araştırmalar %10-15 arasında nikel içeren kaplamaların
optimum korozyon dayanımı, kaynaklanabilirlik ve süneklik özellikleri sergilediklerini
göstermiştir.
Elektrolitik kaplamalarda azalan kaplama kalınlığı ile kaynaklanabilirlik kabiliyeti artmaktadır.
Saf çinko kaplamalara nazaran çok daha ince kalınlıklarda çinko-nikel kaplamalar eşdeğer ve hatta daha yüksek korozyon dayanımı sergilemekte,
bu doğrultuda kaynaklanabilirlik kabiliyeti de artmaktadır.
Bu durum çinko-nikel kaplamaların kaynak gerektiren uygulamalarda tercih edilmesini sağlar.
Çinko-nikel alaşımlarının bir başka avantajı, kaplanan bileşenlerin şekillendirilmesinden ve ısıl işleminden sonra korozyon dirençlerinin %60 ila %80'ini muhafaza etmeleridir.
Bu özellik, bu alaşımları bağlantı elemanları, fren ve yakıt hatları ve diğer kaput altı bileşenler gibi otomotiv uygulamaları için uygun hale getirir.
Çinko-nikel kaplamaların alkali formülasyonları, kullanım kolaylıkları ve özellikle borularda
ve parçaların iç konfigürasyonlarında daha düzgün alaşım bileşimi ve daha iyi genel
korozyon direnci sağladıkları için tercih edilir.