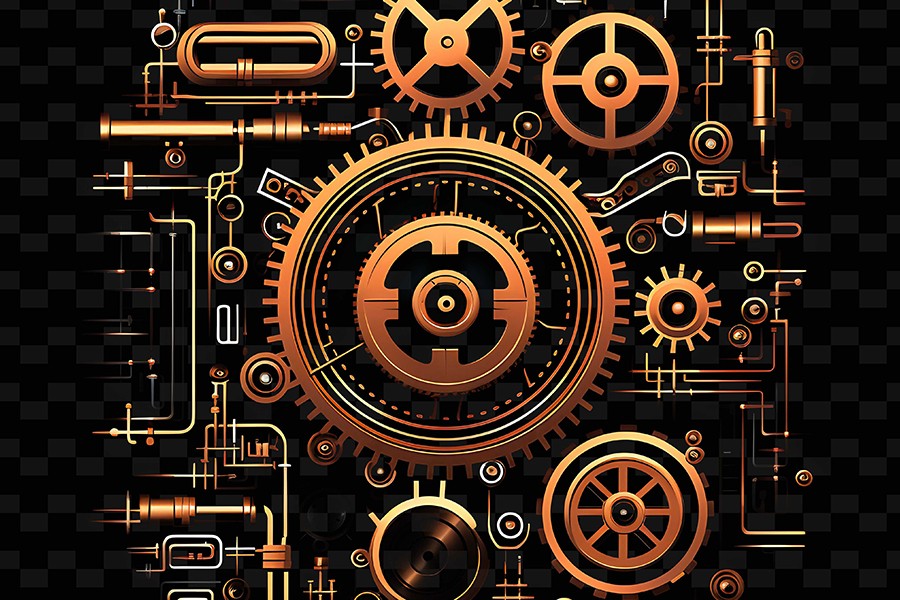
The development and control of the quality of a metal product begins at the designer's desk. The metal finisher (coater) is limited in what he can do within certain principles of mechanical design and electroplating. The technical responsible must understand the constraints regarding the geometries and shape of the workpieces to ensure the desired quality at acceptable costs. The designer can put at least as much effort into the achievable finish quality of the workpiece as the coater.
Important surfaces can be defined as surfaces that are visible (reflected) in the coating literature and where the risk of rusting is undesirable.
In order to improve the coating quality and the final processing appearance of the product, as well as reduce costs; The issues that the product designer should take into consideration can be listed as follows:
For polishing, polishing and sanding operations;
- Blind holes, recesses and connection slots should be avoided.
- Complex surface geometries should be avoided.
- Important surfaces must be easily accessible.
- Sharp edges and protrusions should be avoided.
For a good coating distribution;
Experience and cost accounting have shown that surface treatments of simple shapes can always be done more smoothly and economically than complex shapes. This is the number one rule for the designer of the product. For important surfaces, the most important factor determining quality is the thickness of the coating. Due to the basic rules of electrochemistry, a particle of any shape or size cannot be coated with perfect dispersion. Portions of the workpiece closer to the anodes accept a thicker coating layer. Sharp corners and protrusions tend to absorb most of the electrical current supplied. The goal of the coating designer is to reduce thickness distribution variations on important surfaces as much as possible and simultaneously avoid unnecessary thickness build-ups on unimportant surfaces.
Empirical rules and models; It can guide the designer in terms of coating thickness distribution, economy and quality. The principles obtained from practical experience can be listed as follows;
- Concave and flat surfaces should be avoided. Convex surfaces accept more uniform coating.
- Indents and protrusions should be softened with a wide radius. Concave cavities and slots should be avoided.
- The number of blind holes should be kept to a minimum, as ensuring the minimum coating thickness inside these holes can be problematic. The depth of blind holes should not be more than half the hole diameter and holes smaller than 6 mm should be avoided.
- To avoid installation problems after coating, countersunk holes must be drilled in the fasteners.
- If there are protrusions and ribs, their heights should be low and their radii should be wide.